Gaskets 101
Everything You Need To Know
Gaskets are ubiquitous—they're found in workplaces, vehicles, and even smartphones. They act as seals or grommets that join two components together.
Gaskets can be made from rubber, plastic, metal, or other materials, tailored to specific needs. At A.R. Thomson Group Inc, we have extensive experience working with a wide range of gasketing materials to create custom products.
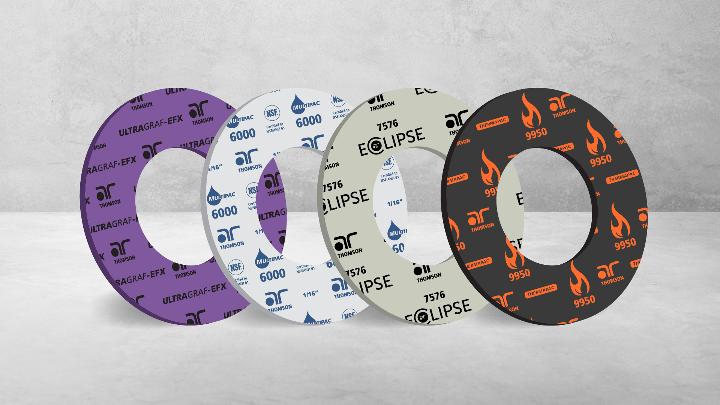
As you explore further, you'll discover that gaskets offer more than just leak prevention. But before you get overwhelmed trying to differentiate between various types, let us guide you through and provide insights for your projects.
Definition of a Gasket:
A gasket is a mechanical seal that fills the space between two mating surfaces, typically to prevent leakage from or into the joined objects while under compression. Gaskets are commonly made from flexible materials such as rubber, silicone, metal, or various composite materials. They are used in a wide range of applications, including automotive engines, piping systems, machinery, appliances, and electronics, to provide a secure and leak-resistant seal.
How are Gaskets Tested?
Gaskets undergo various testing methods to ensure their effectiveness and reliability. Some common tests include:
Compression Test: Gaskets are subjected to compressive forces to simulate real-world conditions and verify their ability to maintain a seal under pressure.
Leakage Test: Gaskets are exposed to fluids or gases at different pressures to assess their resistance to leakage.
Chemical Resistance Test: Gaskets are exposed to various chemicals to determine their resistance to corrosion, degradation, or swelling.
Temperature Resistance Test: Gaskets are exposed to extreme temperatures to assess their ability to maintain their integrity and sealing properties under different thermal conditions.
Fluid Immersion Test: Gaskets are submerged in fluids to evaluate their resistance to immersion and their ability to maintain a seal over time.
Compression Set Test: Gaskets are compressed for a specified period and then measured to assess their ability to recover their original shape and sealing properties after compression.
Aging Test: Gaskets are subjected to accelerated aging conditions, such as exposure to UV radiation or ozone, to evaluate their long-term durability and performance.
These tests help ensure that gaskets meet the required standards and specifications for their intended applications, providing reliable sealing solutions in various industries.
Gasket or Seal?
Gaskets and seals play vital roles in ensuring the integrity and functionality of mechanical systems by preventing the leakage of fluids or gases. While the terms are often used interchangeably, they serve distinct purposes. A gasket serves as a mechanical seal specifically designed to fill the space between two mating surfaces, creating a barrier against leaks under compression. On the other hand, seals encompass a broader range of components or mechanisms used to close off or secure openings, including gaskets, O-rings, lip seals, and mechanical seals, each serving unique sealing functions based on application requirements. Understanding the differences between gaskets and seals is crucial for selecting the appropriate solution to achieve effective sealing and system performance in various industrial applications.
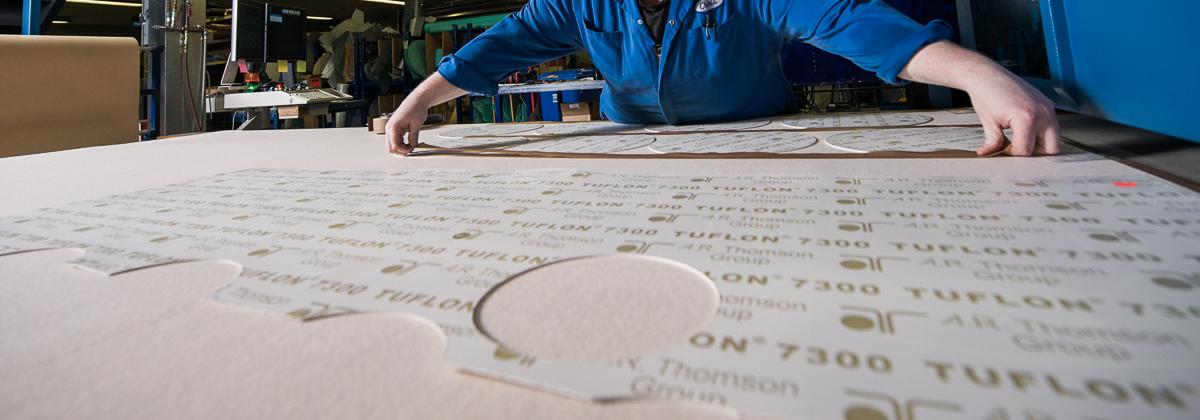
Properties of a Gasket:
Gaskets possess several key properties essential for their effective performance in sealing applications. These properties include:
Compressibility: Gaskets are designed to deform and conform to irregularities on mating surfaces, ensuring a tight and uniform seal under compression.
Resilience: Gaskets exhibit resilience to maintain their sealing integrity even after being compressed or subjected to varying pressures, temperatures, and environmental conditions.
Chemical Resistance: Gaskets are often made from materials that resist degradation or swelling when exposed to various fluids, chemicals, and solvents, ensuring long-term sealing performance.
Temperature Stability: Gaskets are engineered to withstand a wide range of temperatures, from extreme cold to high heat, without compromising their sealing properties or integrity.
Creep Resistance: Gaskets demonstrate resistance to creep, which is the gradual deformation or flow of material under constant load, ensuring that the seal remains intact over time.
Compatibility: Gaskets are selected based on their compatibility with the mating surfaces and the fluids or gases being sealed, preventing contamination or leakage.
Durability: Gaskets are engineered to withstand mechanical stresses, vibrations, and environmental factors, ensuring long-term durability and reliability in demanding applications.
By possessing these properties, gaskets effectively fulfill their role as essential sealing components in various industries, including automotive, aerospace, manufacturing, and petrochemical.
When are Gaskets used?
Gaskets are used in a wide range of applications across numerous industries where the need for a reliable seal between mating surfaces arises. Some common instances where gaskets are utilized include:
Automotive: Gaskets are employed in engines, exhaust systems, transmissions, and various components to prevent leaks of fluids such as oil, coolant, and exhaust gases.
Industrial Machinery: Gaskets are integral in sealing joints and connections in pumps, valves, compressors, and hydraulic systems, ensuring efficient operation and preventing fluid leakage.
Plumbing and Piping Systems: Gaskets are utilized in pipe flanges, fittings, and connectors to create leak-tight seals in plumbing, HVAC systems, and industrial piping networks.
Aerospace and Aviation: Gaskets play a critical role in sealing fuel systems, hydraulic systems, and aircraft engines to maintain safety, reliability, and operational efficiency.
Electrical and Electronics: Gaskets are used in electronic enclosures, circuit boards, and electrical panels to provide protection against moisture, dust, and electromagnetic interference.
Pharmaceutical and Food Processing: Gaskets are employed in equipment and machinery used in pharmaceutical manufacturing and food processing to maintain hygienic conditions and prevent contamination.
Marine and Offshore: Gaskets are utilized in marine engines, hull fittings, and offshore drilling equipment to withstand harsh marine environments and prevent leakage of fluids.
Overall, gaskets are essential sealing components in a diverse array of applications where maintaining fluid containment, environmental protection, and operational integrity are paramount concerns.
8 Types of Gaskets and Materials
There are various types of gaskets available, each designed for specific applications and operating conditions. Here are eight common types of gaskets along with the materials they are typically made from:
Rubber Gaskets: Made from materials such as neoprene, EPDM, or nitrile rubber, these gaskets are suitable for sealing applications involving water, air, or moderate chemicals.
Cork Gaskets: Composed of cork material, these gaskets are commonly used for sealing against oil, fuel, and automotive fluids due to their resilience and compatibility with petroleum-based substances.
Metallic Gaskets: Constructed from materials such as stainless steel, aluminum, or copper, metallic gaskets provide high-temperature and high-pressure sealing solutions, often used in industrial and petrochemical applications.
Spiral Wound Gaskets: These gaskets feature a combination of metal and filler material, such as graphite or PTFE, wound in a spiral pattern, providing excellent resilience and adaptability to flange irregularities in high-pressure and high-temperature environments.
Non-Asbestos Gaskets: Designed as alternatives to traditional asbestos gaskets, these gaskets are made from synthetic fibers bonded with elastomers, offering superior resistance to heat, chemicals, and corrosion.
PTFE Gaskets: Constructed from polytetrafluoroethylene (PTFE), commonly known as Teflon, these gaskets exhibit exceptional chemical resistance, low friction, and non-stick properties, suitable for sealing applications involving aggressive chemicals and extreme temperatures.
Graphite Gaskets: Manufactured from flexible graphite material, these gaskets provide excellent thermal stability, chemical resistance, and sealability, making them ideal for high-temperature and corrosive environments.
Silicone Gaskets: Made from silicone rubber, these gaskets offer exceptional flexibility, temperature resistance, and weatherability, commonly used in automotive, electrical, and food processing industries.
Each type of gasket material possesses unique properties suited to specific applications, ensuring reliable sealing performance across various industries and environments.
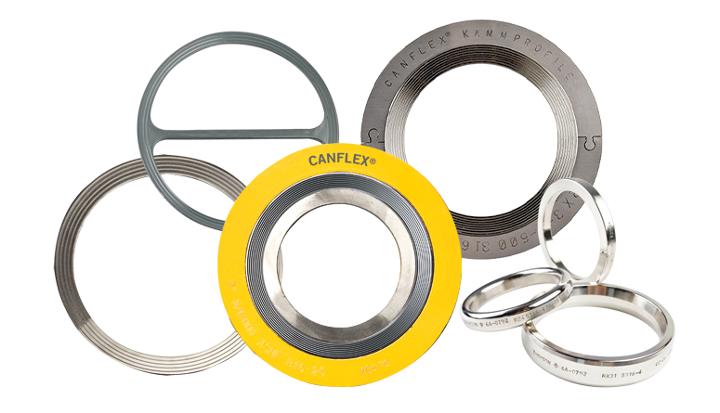
Common Types of Gaskets
Flat Gaskets: These are simple, flat-shaped gaskets typically made from materials like rubber, cork, or paper. They're used in low-pressure sealing applications.
Ring Gaskets (or O-Rings): Circular gaskets made from materials like rubber or silicone. They're commonly used in dynamic sealing applications, such as hydraulic systems and pipe fittings.
Spiral Wound Gaskets: These gaskets feature a V-shaped metal strip wound with a filler material, often graphite or PTFE. They're suitable for high-pressure and high-temperature applications, such as flange connections in pipelines.
Metal Jacketed Gaskets: These gaskets consist of a metal jacket with a soft filler material, providing both strength and flexibility. They're used in applications requiring resistance to high pressures and temperatures, such as heat exchangers and reactors.
Kammprofile Gaskets: These gaskets feature a serrated metal core with a soft filler material, providing excellent sealing under high pressures and varying temperatures. They're commonly used in flanged joints in oil and gas industries.
Rubber Gaskets: Made from materials like neoprene, EPDM, or nitrile rubber, these gaskets are flexible and resistant to various fluids, making them suitable for sealing applications in automotive, plumbing, and machinery.
Cork Gaskets: Composed of cork material, these gaskets are resilient and often used in sealing against oil and automotive fluids, such as in engine gaskets and transmission seals.
PTFE Gaskets: Constructed from polytetrafluoroethylene (PTFE), these gaskets offer exceptional chemical resistance and low friction properties, making them suitable for sealing applications involving aggressive chemicals and extreme temperatures.
These gasket types cover a wide range of applications and industries, providing solutions for various sealing needs.
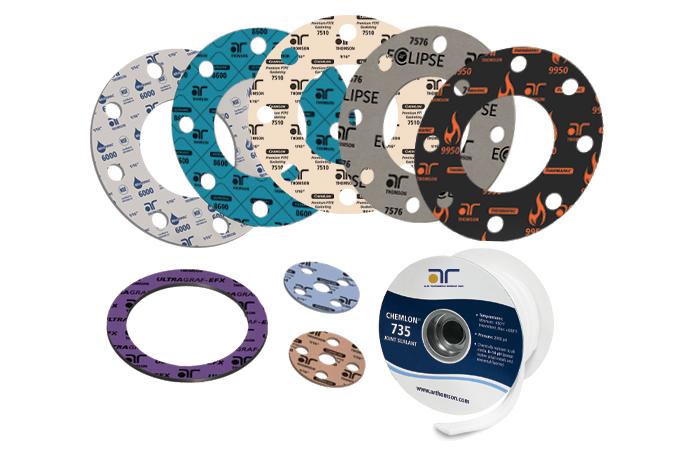
About A.R. Thomson Group Inc.
A.R. Thomson Group Inc. has been manufacturing and supplying gaskets and sealing products since 1967 to a wide range of customers throughout Alberta, British Columbia, Ontario, Quebec and Saskatchewan.
We are a customer orientated company serving customers with innovative fluid sealing products and services that provide reliability, cost savings and process safety.
With our manufacturing division we have the capability to produce gaskets in-house in an extensive variety of styles and a wide assortment of materials. Our highly trained & experienced staff are ready to handle all your gasket requirements from three convenient locations: Surrey, Edmonton and Sarnia.
Want more information? Contact us today.