Products > Mechanical Seals
Mechanical Seals Supply - Pumps & Rotating Equipment
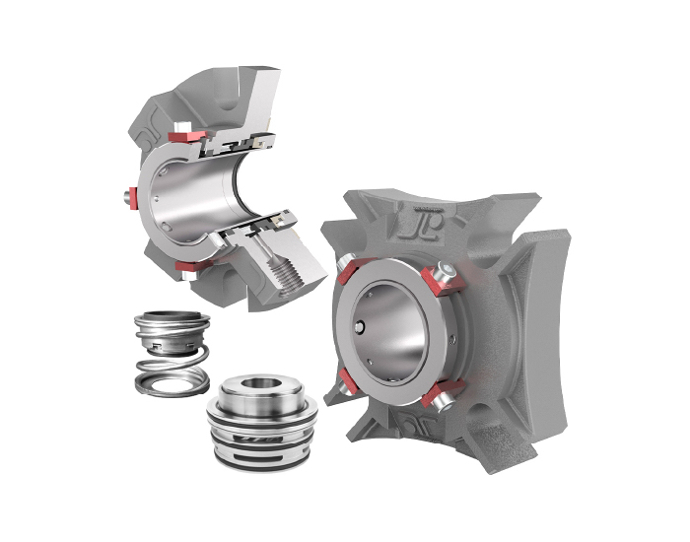
A.R. Thomson Group Inc. offers a comprehensive range of mechanical seals designed to handle the most demanding industrial applications, providing customers with high-quality and reliable sealing solutions. With our on-site experience and expertise, A.R. Thomson Group Inc. offers technical support, prompt delivery, and personalized service, ensuring customers receive the right mechanical seals and the assistance they need for successful installation and operation.
Quality Assured:
A.R. Thomson Group Inc. maintains an ISO 9001:2015 Quality Management System. Manufacturing, assembly and distribution of CNC cut products, gaskets, sealing products and fasteners, distribution of instrumentation valves and fittings, and repair of mechanical seals.
Standard Stock Mechanical Seals:
- Standard Cartridge Spring Seals
Standard cartridge seals are pre-assembled mechanical seals designed for common industrial applications, offering a convenient and efficient solution by integrating all the necessary sealing components into a single, easily replaceable unit.
- API Cartridge Seals
The 9000 series pusher seals are all stationary flexible element as a standard. Available in single and dual cartridge. Mechanical seals for the oil & gas industry. - Split Seals
Single and double split seals. - Special Duty
Slurry, gas liftoff, mixer. - Single Spring Seals
Component style seals to replace most common OEM designs. -
Bellows
Chem Pro, TBH, TBS.
- Mechanical Seal Repair
Repairs, seal face refurbishment, seal reconditioning, reverse engineering, material upgrades, performance enhancement, custom solutions and seal failure analysis. - Seal Replacements for major brands
John Crane, Flowserve, AES, Chesterton, Eagle Burgmann and More.
Downloads:
Standard Cartridge TAC Brochure
Mechanical Seal Repair Brochure
Question: What Does A Mechanical Seal Do?
A mechanical seal is a critical component used in various rotating equipment, such as pumps, compressors, and agitators, to prevent leakage of fluids or gases between the rotating shaft and the stationary housing. It serves as an effective and reliable sealing solution to contain the internal pressure of the equipment and prevent external contaminants from entering the system. Here's what a mechanical seal does:
1. Prevents Leakage: The primary function of a mechanical seal is to prevent leakage along the rotating shaft. It creates a barrier between the high-pressure process fluid inside the equipment and the external environment. By maintaining this seal, it ensures that the process fluid or gas remains contained and doesn't escape, avoiding potential hazards and environmental issues.
2. Maintains Efficiency: A well-functioning mechanical seal is crucial for maintaining the efficiency of the equipment. By reducing or eliminating leakage, the system can operate at its designed capacity, ensuring optimal performance and minimizing energy losses.
3. Handles Different Fluids: Mechanical seals are designed to work with various types of fluids, including water, oil, chemicals, and gases. They can be customized with different materials and configurations to handle specific fluid characteristics and operating conditions.
4. Adapts to Operating Conditions: Mechanical seals are versatile and can adapt to a wide range of operating conditions, such as varying temperatures, pressures, and rotational speeds. Depending on the application, seals can be chosen to withstand extreme conditions, ensuring reliable performance across different environments.
5. Extends Equipment Life: By preventing fluid leakage and reducing wear and tear on the equipment, mechanical seals contribute to extending the lifespan of rotating machinery. They help to protect the shaft and other critical components from corrosion and erosion caused by contact with the process fluid.
6. Reduces Maintenance Costs: Reliable mechanical seals require less frequent maintenance compared to traditional packing seals. This leads to reduced downtime and maintenance costs, making them a cost-effective sealing solution in the long run.
7. Increases Safety: Mechanical seals play a vital role in ensuring the safety of personnel and the environment. By containing hazardous or volatile substances, they help prevent accidents, spills, and leaks that could pose health and environmental risks.
8. Minimizes Product Contamination: In applications where product purity is crucial, such as food and pharmaceutical industries, mechanical seals provide an effective barrier to prevent contamination from external sources.
9. Accommodates Shaft Movement: Rotating equipment experiences shaft movement due to thermal expansion or other factors. Mechanical seals are designed to accommodate these movements while maintaining a reliable seal, ensuring smooth operation of the equipment.
In summary, a mechanical seal is an essential component that ensures the efficient and safe operation of rotating equipment by preventing fluid leakage, minimizing downtime, reducing maintenance costs, and extending the equipment's lifespan. Its ability to adapt to various operating conditions and handle different fluids makes it a widely used sealing solution in numerous industrial applications.