Products > Gaskets
Gaskets & Sealing Products
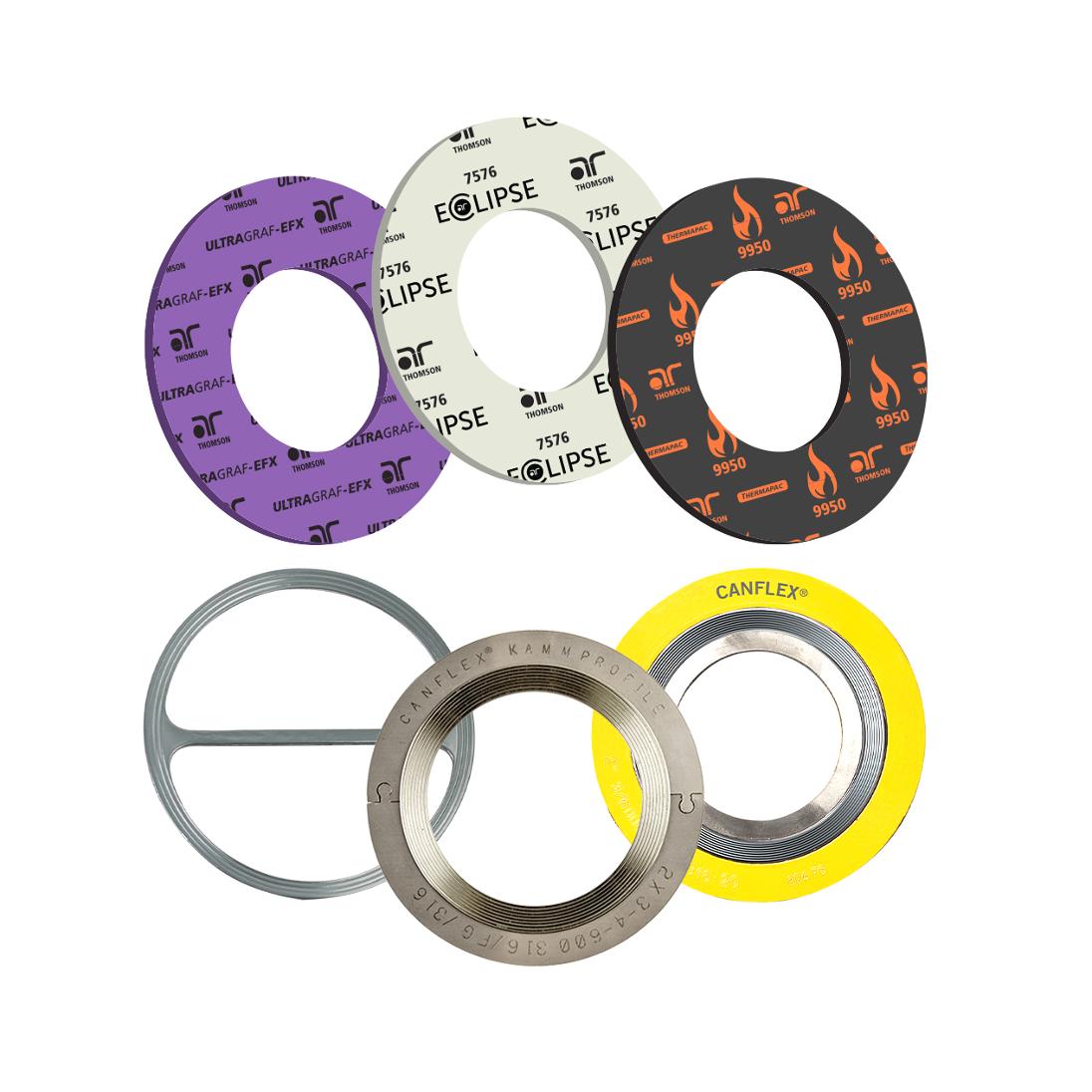
A.R. Thomson Group Inc. was established in 1967 as a Canadian manufacturer & distributor of gaskets and other fluid containment products. No matter what your gasket and sealing needs, we can help.
Quality Assured:
A.R. Thomson Group Inc. maintains an ISO 9001:2015 Quality Management System manufacturing, assembly and distribution of CNC cut products, gaskets, sealing products and fasteners, distribution of valve products and fittings, and repair of mechanical seals.
A.R. Thomson Group Inc. Gaskets:
- Non-Metallic Gaskets & Sheets
Compressed Sheet Gaskets - Thomson Multipac™, Thermapac, cork, cork rubber blends, gasket tapes, Teflon® Chemlon®, Garlock®, Gore®, rubber materials and flexible graphite. - High Pressure / Temperature Compressed Gaskets
Compressed and graphite sheet for steam service, hot water, mild chemical, fire-safe rated, high temperature dry gas, and air service.
- All-in-one Chemical Service Gasket
Eclipse® 7576, PTFE gasket with universal chemical compatibility, low stress to seal, maximum load retention and outstanding rigidity for easy installation. -
Next Generation Compressed Sheet and Flexible Graphite Gaskets
Ultrapac ® , compressed gasketing with a blend of graphite fibers, inorganic fillers and NBR binders. Ultragraf®, flexible graphite sheet with unique Flexmet 316LSS insert.
- Canflex® Spiralwound GasketsRW, RWI, CW and CWI gaskets. MC and MCR gaskets for manhole cover assemblies.
- Canflex® Kammprofile Gaskets
Manufactured from solid metal, CANFLEX® kammprofile gaskets combines all of the desirable qualities of a solid metal gasket with the added advantages of a reduced area of contact. 942 A, 942 AR, 942 AR2.
- Thomson Ring Joint Gaskets
API 6A, manufactured in RX, BX, R Oval and Octagonal. Custom profile gaskets and lens rings are also available
upon request. - Canflex®
High Temperature Gaskets (THT)
High temperature THT protects the flexible
graphite from oxidation at elevated temperatures.
-
Other Metal Gaskets
Corrugated solid metal, double-jacketed, double-jacketed corrugated, double-jacketed corrugated with corrugated metal filler, solid metal, solid metal profile. All common metals, exotic alloys and filler materials in all configurations for the most extreme applications.
- NSF 61 Gaskets
4500 EPDM, Multipac™ 6000 compressed and Toruseal molded rubber gaskets. - OptiLoad Gaskets
Aflas, Epdm, FKM Max, T-Shield.
Downloads:
Next Generation Gasket Brochure
Metal Gaskets Canflex Brochure
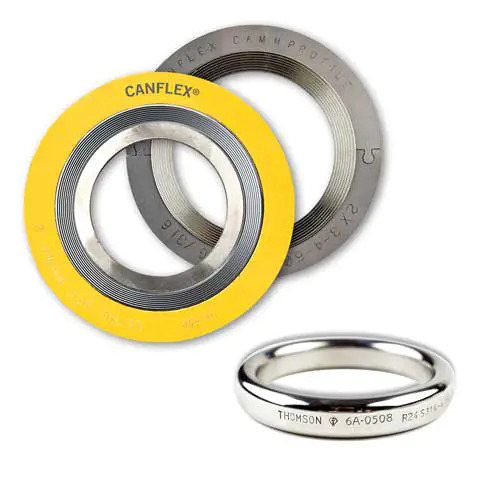
Metallic Gaskets
These include the Spiral Wound and Kammprofile designs using stainless steel and exotic alloys. Our offerings extend to a diverse range of high-temperature and chemically resistant fillers and facings, featuring flexible graphite, vermiculite, and PTFE (Teflon™).
Browse Metallic
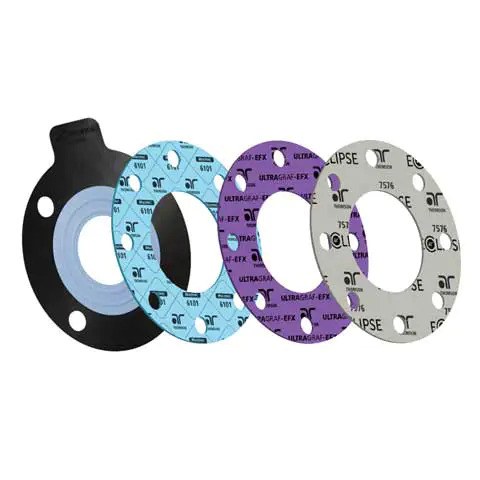
Non-Metallic Gaskets
The Thomson Performance Sealing range encompasses a diverse selection of products, including compressed sheet material, Teflon™ (PTFE), and elastomeric options. These are designed to meet the requirements of demanding industrial applications
Browse Non-Metallic
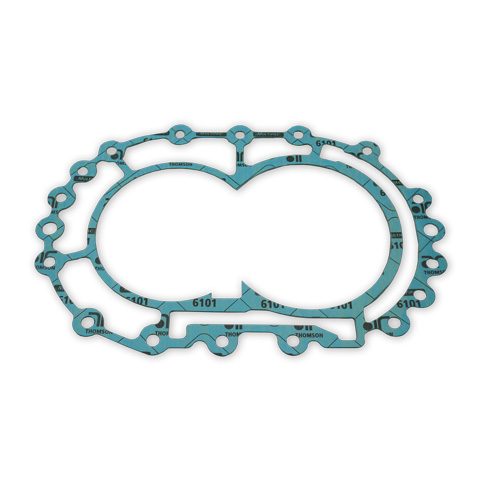
Custom Gaskets
We specialize in crafting custom-cut gaskets and seals from a variety of materials, including compressed sheet, rubber, flexible graphite, and Teflon. In addition, we provide molded rubber products and rubber extrusions tailored to meet customer specifications.
Custom
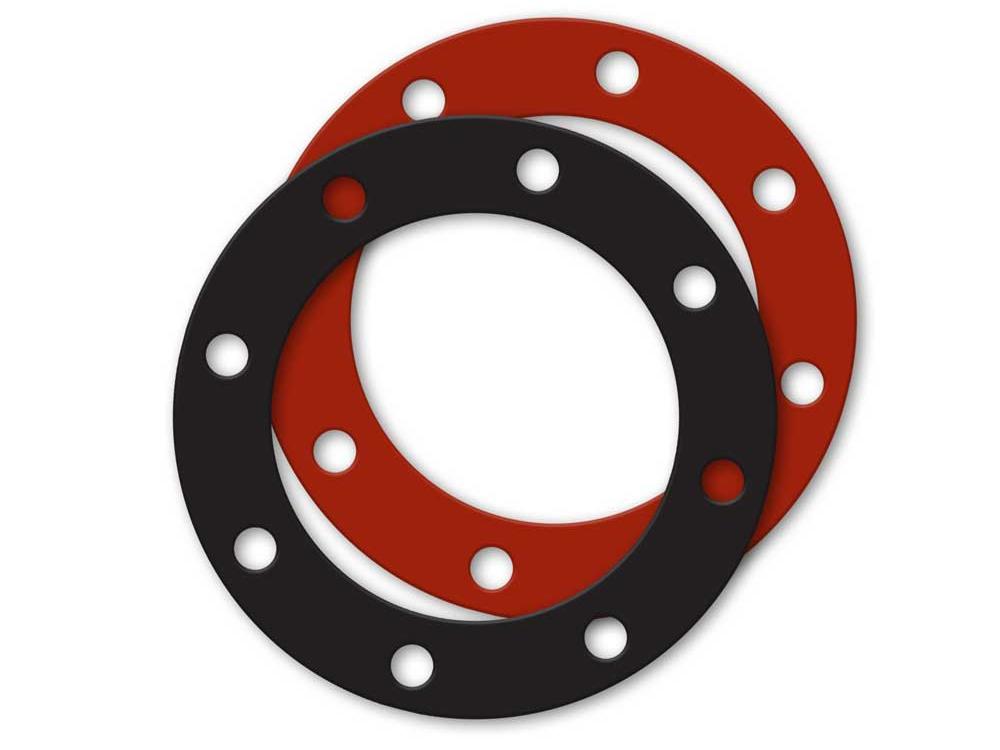
Rubber Gaskets
Wide selection of rubber, bulk rolls and sheet. Nitrile, Neoprene, Silicon, Viton, Aflas EPDM, NSF 61 certified and much more - in stock, and ready to ship.
Learn More
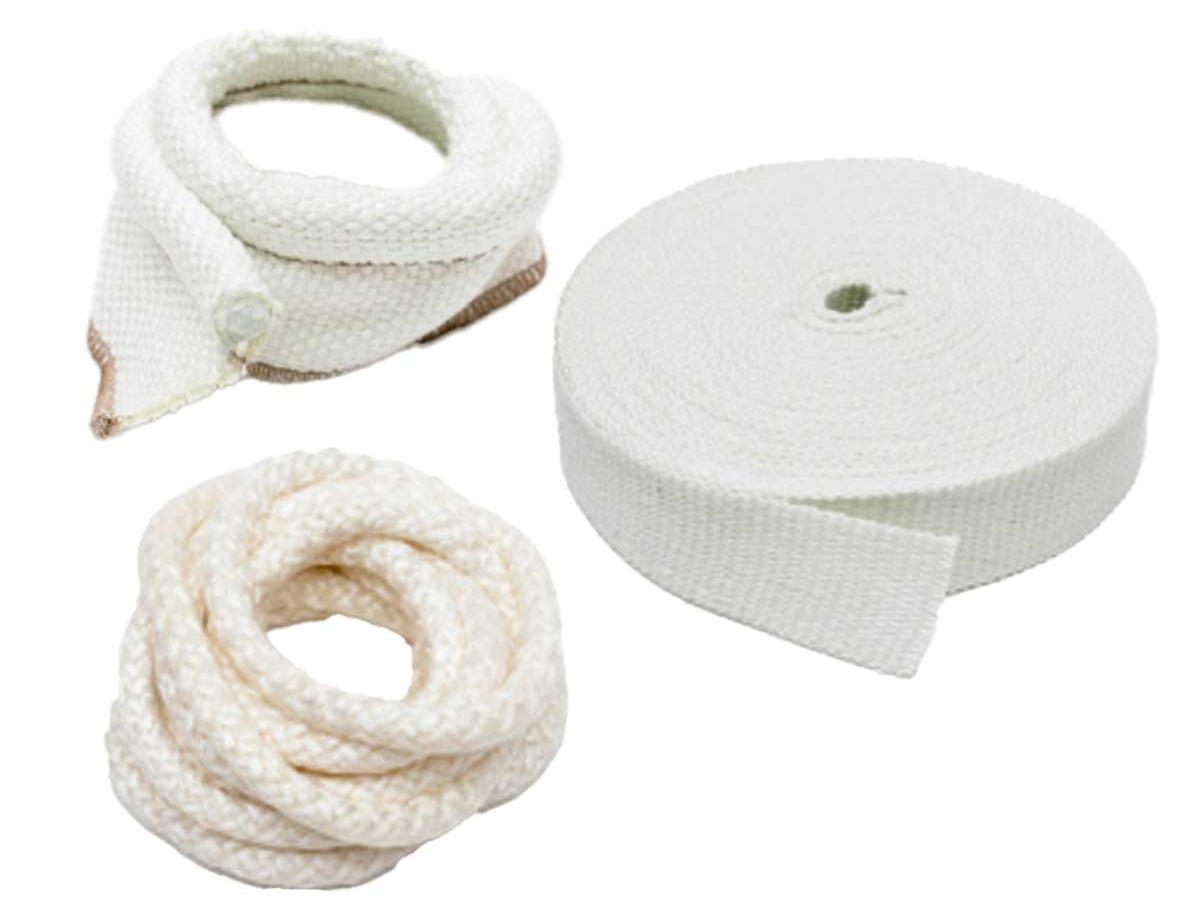
Textiles Product
High temperature fiberglass braided rope ceramics, tadpole tape, drop warp tape, door seals, boilers and more.
Learn More
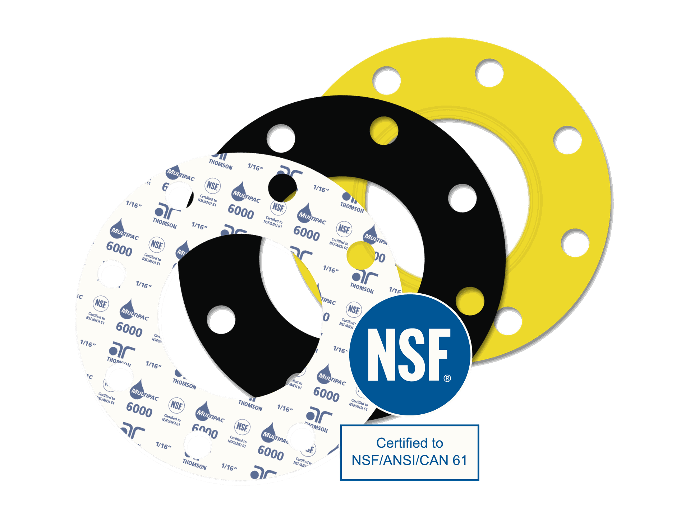
NSF 61
NSF 61 is made from materials that have been certified to comply with the NSF/ANSI/CAN Standard 61 for drinking water. A.R. Thomson Group is a certified NSF fabricator.
Learn More